International Paint has introduced Interline 9001, a new Bimodal Epoxy coating for the cargo tanks of chemical tankers. With enhanced cargo resistance, zero absorption for many cargoes and fewer cycling restrictions, Interline 9001 simplifies the carriage of a wide range of liquid cargoes, optimizing vessel earning potential.
Wednesday, March 30, 2011
Modern chemical tankers of IMO Ship type I, II and III are designed and equipped to handle a very wide range of liquid cargoes ranging from relatively innocuous materials such as vegetable oils to more aggressive types such as ethylene dichloride and caustic soda. Most vessels will have coated mild steel tanks, stainless steel tanks or a combination of both.
The most commonly used type of coating on mild steel tanks is Epoxy Phenolic, which provides broad cargo carriage capability but can absorb and retain certain cargoes. This can create a difficult cleaning challenge to remove any absorbed cargo and thus minimize the risk of contaminating subsequent cargoes. A ‘recovery period’ may also be required. All of this can incur significant expense for a ship operator in terms of time and money
The next most common type is Zinc Silicate. These coatings provide excellent resistance to solvents and pure chemicals but are limited in their use due to an inability to resist acids and alkalis. The rough surface of Zinc Silicate coatings can also be difficult to clean, again costing time and money.
Costs of on board cleaning are significant. Bunkers for hot water for example could mean a tank cleaning operation alone adding over $100,000 to operating expenses for one full vessel clean and this doesn’t take into account manpower or costs of cleaning materials.
Interline®9001 is designed therefore to deliver greater efficiency and flexibility in the operation of chemical tankers, easily switching from one cargo to the next with minimal downtime. It can carry all of the cargoes standard epoxy phenolic technology can, plus a further 25% of the large volume cargoes that it cannot and has over 60% fewer cycling restrictions.
The technology opens up new (previously restricted) cargo sequences for the carriage of aggressive cargoes, for example, methanol to fatty acids to ethylene dichloride back to back, with no coating recovery required.
Its low cargo absorption profile reduces the risk of contamination between cargoes and combined with its smooth, glossy surface, can cut cleaning time and materials by up to 70% compared to standard epoxy phenolics or zinc silicates.
With reduced cleaning requirements, comes a corresponding reduction in fuel and CO2 emissions. In addition, a low volatile organic content (VOC) and 80% volume solids helps to enhance operator environmental profile.
Based on Bimodal Epoxy technology, Interline®9001 is a carefully engineered blend of polymers. Firstly, a special combination of low and high molecular weight polymers creates a loosely bound, but highly crosslinked flexible network chain on ambient curing. The post cure process then locks these network chains firmly together to provide a highly chemical resistant paint film offering low absorption properties and easy clean whilst still maintaining flexibility to ensure crack resistance on welds when subjected to vessel flexing.
Mr. G. Johnson, L&I Maritime (UK) Ltd. (consultancy services to the chemical tanker market), said, “Having assessed the cleaning properties of Interline®9001 in a range of cargoes and in accordance with the Dr. Verwey Tank Cleaning Guidelines*, it is evident that compared to the industry standard epoxy phenolic and zinc silicate systems, Interline®9001 is easier and quicker to clean. Furthermore, there is data to support the claim that when Interline®9001 is cleaned in direct accordance with Dr. Verwey or by up to 70% less than Dr. Verwey recommends, the level of cleanliness achieved is the same. This will likely translate into considerable savings in time, materials and manpower for vessel operators when cleaning from one cargo to the next.”
This level of efficiency means that a typical 45k DWT vessel could reduce its CO2 emissions by up to 400 tonnes everytime it carries out a full vessel clean.
Mr. Andrew Hopkinson, International Paint Business Development Manager said, “Interline®9001 is the result of working very closely with customers to fully understand their needs whilst engaging cutting edge research in our dedicated tank lining laboratory. Our detailed knowledge of the most aggressive cargoes, together with our experience in tank coating application, allows us to offer a new product that maximises both operational and environmental efficiency in an increasingly challenging market. We believe Interline®9001 represents a smarter solution to maximising profitability”.
* Dr. A. Verwey is the author and publisher of the well known and worldwide used Tank Cleaning Guide. The 8th edition lists over 400 liquid substances carried in bulk. The cleaning charts give the tank cleaning procedure for each listed product to clean from and to in a matrix form
Contact us
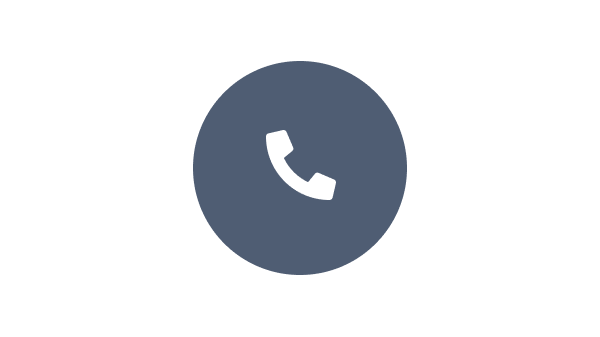
We are here to help
Speak with one of our experts to discuss how we can get the best results for your area of application.
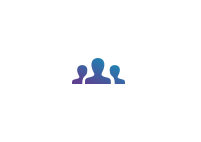
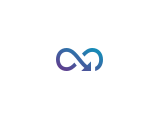
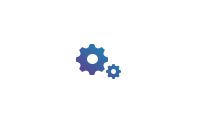