Take a peek into a typical paint locker on board many a merchant vessel today, and as likely as not you’ll find a bit of mess.
Shipboard maintenance seldom warrants the attention that it should. Cosmetic coatings, anticorrosives and thinners fulfil vital functions but hardly hold the same appeal as ultra-smooth, non-stick, go-faster hull coatings which save thousands of dollars a day in fuel bills.
However, the coatings stored in ships’ paint lockers represent a vast market worth around $750 million a year. And as the world fleet hits another record this year, it’s bigger than ever.
Paint lockers are often poorly organised because on-board maintenance is still a relatively low priority for many operators. As a result, coatings – sometimes out of date – vie for disorganised shelf space with various pieces of worn kit used for cleaning, surface preparation and application.
The result is that on-board coatings maintenance often costs more than it should and is certainly not as efficient as it should be. But ship operators today are under more pressure than ever to raise on-board productivity and ensure that the through-life cost of coatings, for example, is kept to a minimum.
Managing seastores
Managers at International Paint plan to tackle this gap in the ongoing maintenance cycle by demonstrating to customers how the adoption of some basic principles could save them money and raise maintenance standards.
These include making sure that a well-ordered maintenance plan is up and running on board; that the right products are selected at newbuilding so that through-life coatings cost can be carefully controlled; and perhaps most importantly, making sure that ships’ crews know how to prepare, apply and maintain on-board coatings effectively by providing expert advice and training.
Even on board well-managed ships, they say, there is often still scope for improvement in procurement procedures, logistics and use of products on board. Ongoing cost savings are, of course, the key objective.
“We want to work really closely with our customers to show that with a little innovation, there are significant savings and wide-scale efficiency improvements to be had,” declares Barry Robison, who heads International Paint’s seastores team. “Effective seastores management is a win for everybody.”
Small refinements … big benefits
“There are plenty of reasons why ship operators should take a look at seastores right now,” he continues. “Today’s markets are as tough as ever and ship operators are highly focused on cost control. At an operational level, there are longer drydocking intervals, shorter port calls and smaller crews.”
“Many seafarers today switch from one company to another,” Barry points out, “and have little knowledge of the many coatings used on board which of course vary from ship to ship. Yet these are the guys who are supposed to maintain on-board coatings to the highest standards.”
“In many cases, there are obvious improvements to be made and small refinements can yield big benefits. On-board maintenance is a continuous function – savings are cumulative.”
Right place … right time
For many, seastores merit little attention because they are just a routine aspect of ongoing shipboard operation, confirms Doug Gilbert, a Technical Manager at International Paint, and specialist in on-board maintenance with many years of coatings experience working for an oil major.
For many, he explains, out of sight is out of mind. But as a result of his experience, he advocates a complete reappraisal of seastores management – from annual budgets to procurement, and from supply logistics to coatings application on board. Streamlined systems promise significant benefits, he says.
Making sure the right products are available in the right quantities, in the right place and at the right time is an obvious starting point, Doug explains. Close co-operation with customers on supply chain optimisation, he says, has already yielded benefits. And making sure that procurement systems work correctly was a key priority stressed by customers in a recent survey undertaken by International.
Now, therefore, the company has reinforced its commitment to an existing key performance indicator. Its “OTIF” initiative – on time and in full – is designed to ensure that customers who wish to embrace the service receive the products they’ve asked for, in appropriate volumes and delivered at the right time. Certainly, International’s global supply network provides a sound foundation for this – the company has 165 dedicated stocking points around the globe supplying more than 500 ports.
Product and customer support
Logistics is of course fundamental, but getting the right products to the right place is only half the story, explains Barry. The company’s product support and after-sales service have been identified by customers as key differentiators. A top priority highlighted by the survey showed the importance of educating ships’ crews and making sure they are using the correct products as effectively as possible.
“We understand the market and have the expertise to provide shipboard personnel with effective on-the-job training,” comments Barry. “A key finding in our recent survey was the importance of product familiarity – seafaring personnel like to know the products they’re using. If we can help to make sure that they are using them correctly, coatings will last longer; smaller volumes will be required; there’ll be less waste; and productivity across the whole process improves as a result.”
As part of its drive to raise seastores efficiency, therefore, International now offers practical support at shipboard level. Much of this focuses on surface preparation and correct application. Doug Gilbert points out that advances in coatings technologies means that today’s products can last longer if they’re used properly.
Effective preparation and application of seastores is more important than ever, he says, and many of today’s on-board coatings issues are a direct result of inexperienced crews.
But International is offering practical support where ships’ crews are shown how best to prepare and apply on-board coatings, with the aim of improving longevity and raising productivity.
More than just the price per litre
Despite the fact that the global seastores market has grown by at least 40% over the last five years, Barry and his colleagues on International’s team are still frustrated that this sector of the coatings market does not receive the priority that it should.
They stress that choosing the right product and getting its application right is far more important in the long run than price per litre today. Yet many ship operators still decide on a 12- or 24-month seastores contract on the basis of price.
But Barry insists that he and his colleagues will be stressing to customers the added value potentially on offer through the company’s seastores efficiency drive.
“Our expertise is available for everyone, and we believe that the cost savings associated with an effective on-board coatings maintenance strategy far outweigh any short-term savings. We know we can save our customers money by looking beyond the product itself. Now, we’re talking to them to explain how. That’s what this initiative is all about!”
If you would like more information on International Paint’s seastores initiative, please contact Barry Robison on email, Twitter or telephone, or reach us on Facebook or Twitter.
Contact us
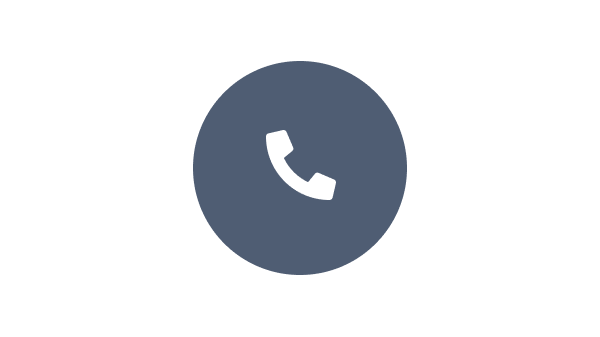
We are here to help
Speak with one of our experts to discuss how we can get the best results for your area of application.
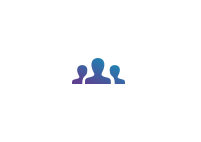
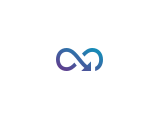
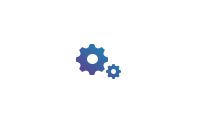