In today’s competitive market, ship owners and operators need clearer guidance on the potential performance benefits of fouling control coatings for their specific vessels to make optimal coating choices. I have outlined the development of models to predict the impact of fouling control coating choices on ship operational efficiency.
Ship owners and operators are sometimes sceptical about comparing the performance claims of different fouling control coatings, partly because the information underpinning the claims can be unclear. As such, there is a need for more accurate and transparent predictions of fouling control performance. In response to this, AkzoNobel has created models predicting the impact of fouling control coating choices on ship powering requirements and operational efficiency. This research aims to provide data that allows owners and operators to compare powering requirement, fuel consumption, cost / benefit and environmental impact analyses for potential fouling control coating choice over the full drydock cycle, empowering them to make the most economical and environmentally optimal choices for their vessels or fleets.
AkzoNobel’s models can be broken down into two main sections. The first section examines how the total hull roughness of a vessel changes over a drydock cycle for each different coating option, as it is affected by the ship’s operational profile. The second section models how total vessel roughness affects total ship resistance, and the resultant powering requirements – essentially, how increased hull roughness impacts performance.
To ensure detail and accuracy, the model for the total roughness change in the first section uses a new total roughness treatment that takes account of the micro and macro roughness of the hull and the impact of biofouling. The model also considers the effect of substrate preparation and coating application choices on surface roughness, and builds on an enhanced understanding of the impact of vessel operational profile, including hull cleaning events and coating performance.
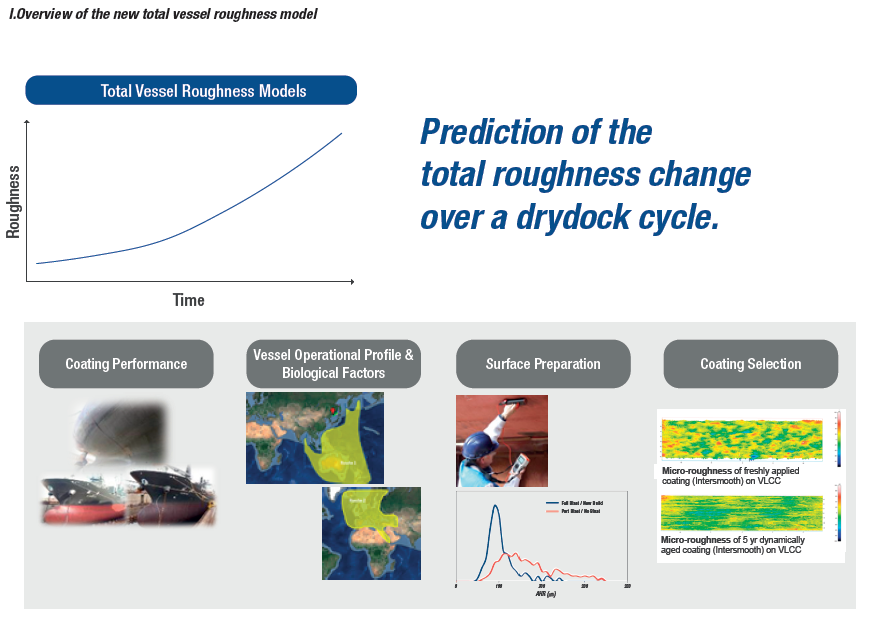
The second section – the correlation of total roughness, total ship resistance and powering requirements is based on new Computational Fluid Dynamics (CFD) resistance and wake field flow models for different representative hull forms. It also factors in optimised ship powering requirement calculations, derivation of speed/power curves as a function of total roughness, and an enhanced understanding of how power requirements are influenced by total roughness. This enables the model to more clearly simulate how hull roughness affects a vessel’s power requirements, and consequently, its fuel consumption.
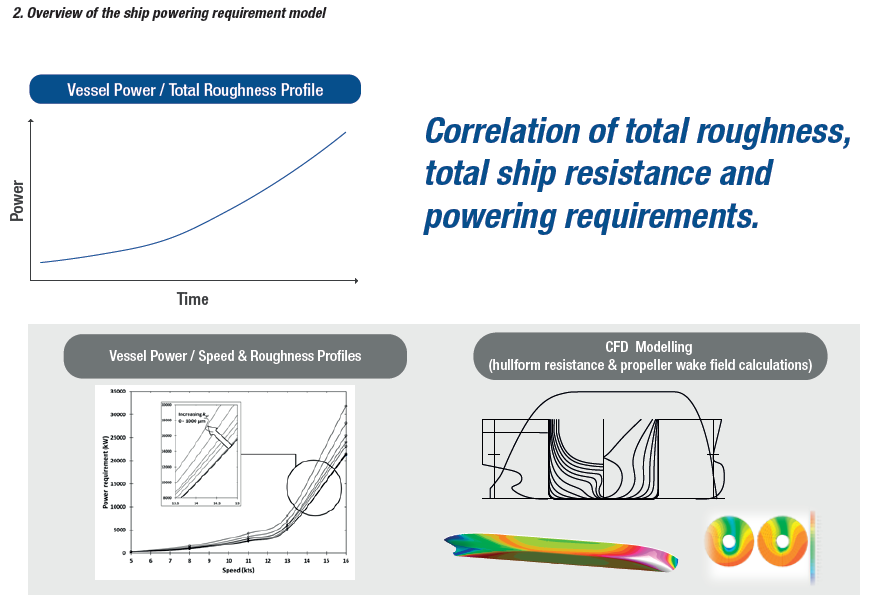
The key outputs of these new models include predictions of vessel powering requirements, fuel oil consumption and cost, greenhouse gas emission predictions and cost benefit analyses over the drydock cycle for each potential fouling control coating choice (see Fig. 3).
As this approach uses observations of past coating performance to predict vessel powering requirements, fouling control coating performance rankings can now be realised as a dollar value for ship owners. It also offers new insights on vessel operational profiles, and allows optimal fouling control choices and hull preparation scenarios to be identified for each individual vessel (or fleet), operational profile and budget.
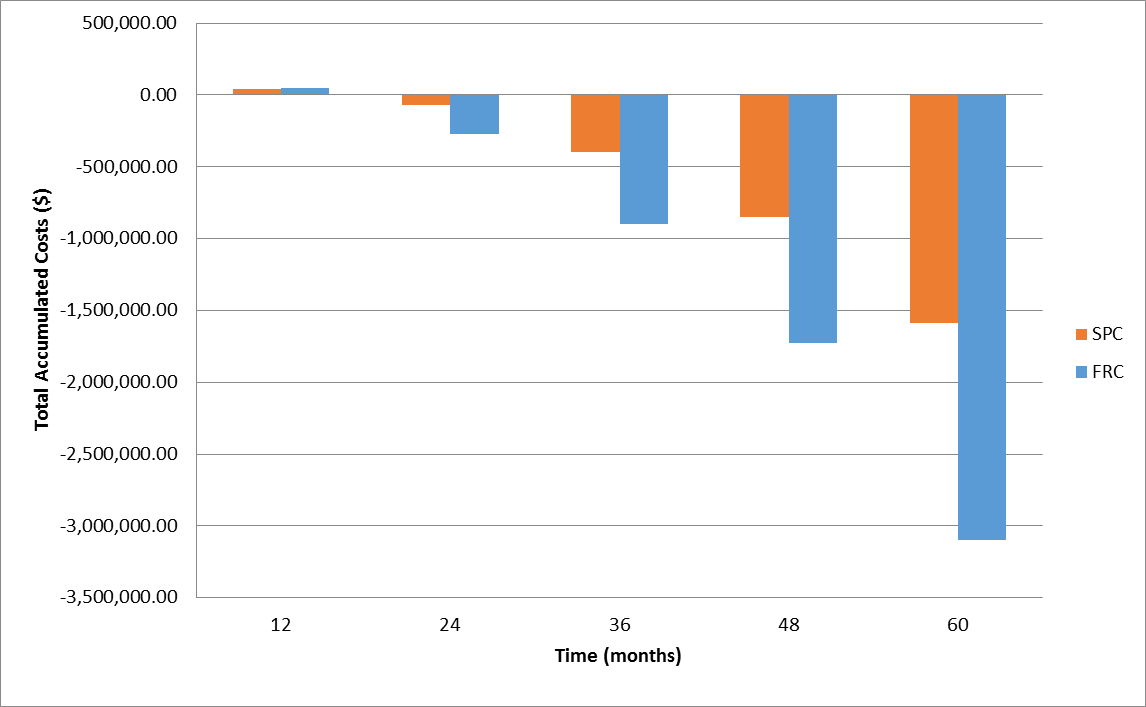
Fig. 3: Total accumulated additional costs (US$) over a 60 month drydock cycle for 1 typical self-polishing copolymer (SPC) and foul release coating (FRC) products relative to a typical controlled depletion polymer (CDP) product when applied to the entire underwater area of 13k TEU/142k DWT containership.
Work to assess the reliability of the new models is well underway, and a substantial dataset comparing model predictions to the actual performance of a wide range of commercial ships is being generated. Early results indicate that the model predictions generally correlate well with reality.
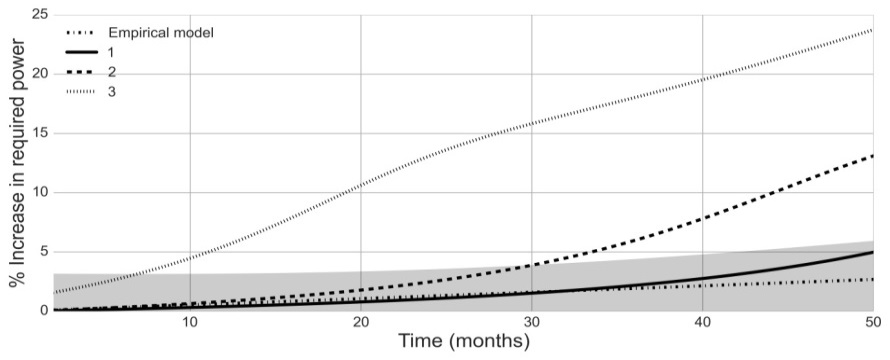
Fig 4: Predicted % increase in required power for a 52k DWT / 4250 TEU containership coated with a typical FRC Coating applied to the entire underwater area default performance scenarios 1 (solid line), overlaid with the percentage power increase determined from the empricial model from the real in-service vessel data (black dots) and the 95% confidence interval for the empricial model (grey shading)
These models are already being used commercially by AkzoNobel through Intertrac Vision, which allows ship owners and operators to make informed decisions regarding fouling control coating selection from both an economic and environmental perspective. Continued improvement in the models that underpin Intertrac Vision will be delivered in-line with expansions in our real-life vessel performance database of fouling control coating performance inspections, Intertrac vessel operation profile and environmental risk databases.
In delivering Intertrac Vision we extract maximum value from our big data and provide meaningful information that our customers require to make informed investment decisions.
Contact us
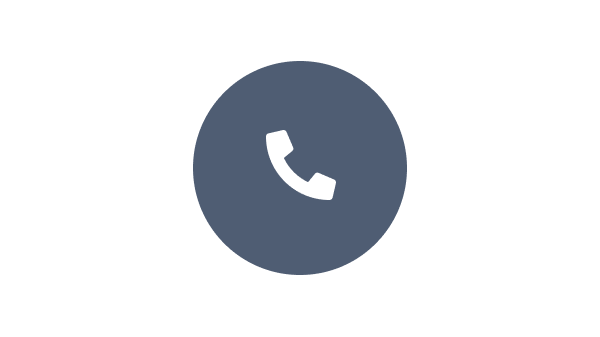
We are here to help
Speak with one of our experts to discuss how we can get the best results for your area of application.
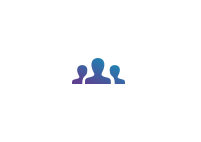
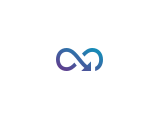
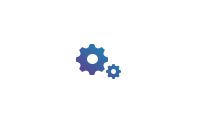