Ships’ hulls coated with AkzoNobel’s premium biocide-based anti-fouling, Intercept 8500 LPP, are revealing excellent and, in some case, exceptional in-service results.
Intercept 8500 LPP is exceeding all expectations. LPP stands for ‘linear polishing polymer’, and this latest addition to our product range, which we launched in March 2016, is doing just that. Its carefully formulated polymer and biocide balance is mirroring both the efficiency and the linear polishing rate for which TBT-based products were favoured.
Unfortunately tributyltin (TBT) had undesired environmental side effects; therefore AkzoNobel (International Paint at that time) was the first marine coatings company to remove TBT from all of their coating products. However, ship operators liked TBT coatings because they polished at a predictable and linear rate over time. We have had our world-leading polymer scientists working on coating formulations that could match the performance of TBT-based products and now, Intercept 8500 LPP is doing just that.
The unique combination of patented Lubyon polymer technology, the self-polishing copolymer silyl methacrylate, and biocide components copper oxide and copper pyrithione have yielded spectacular fouling control results across a range of ship types trading in different regions with a variety of fouling risk challenges.
The coating’s performance is unquestionably the best of all our deep sea biocidal fouling control products and it is particularly suitable for high fouling challenge voyages in regions including the Arabian Gulf and South East Asia. In patch tests, Intercept 8500 LPP has compared very favourably with other biocidal technologies and a premium biocide based competitors’ product. We believe it’s the best in class.
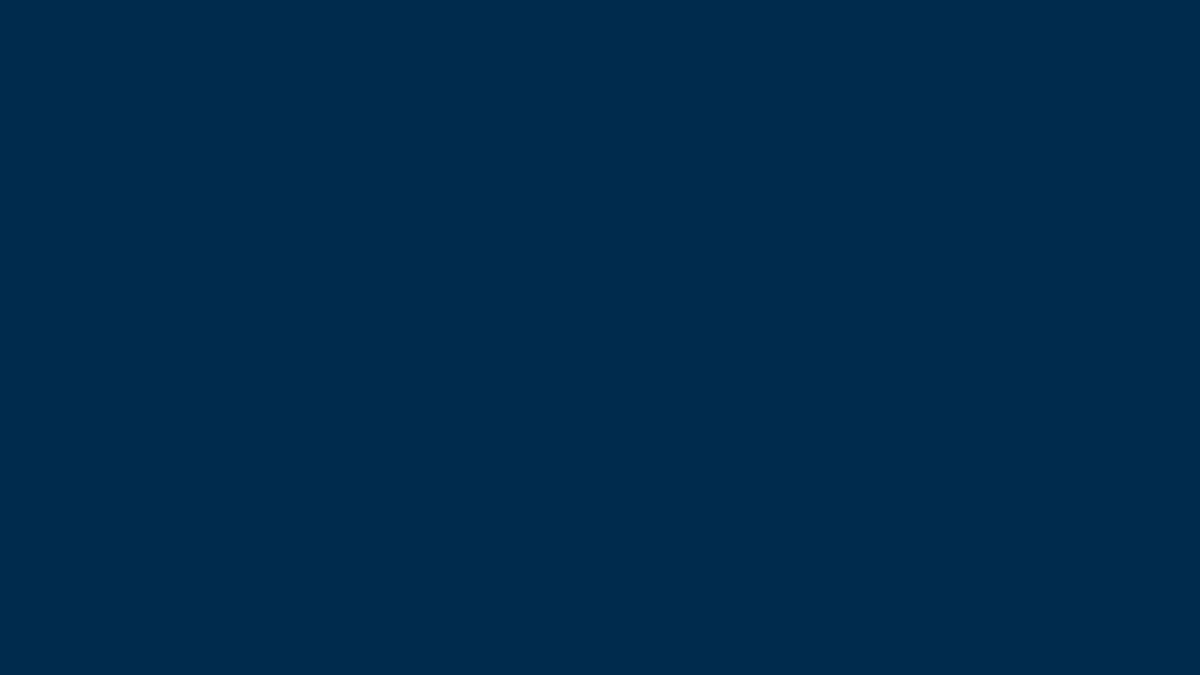
Coating surveys have been carried out on the hulls of various ocean-going vessels including tankers, cruise vessels, container ships and bulk carriers. A test patch on the hull of a 109,229 dwt Aframax tanker for example, was found to be almost free of fouling after 20 months of operation between July 2015 and March 2017.
This was remarkable because the vessel had spent more than 60% of her time in waters of either high or very high fouling risk, and she also had spells of low activity in a weak tanker market. Low activity or, even worse, idle time waiting for cargoes substantially increase hull fouling rates.
In contrast and on the hull of the same tanker, a competitor’s test patch did not perform as well. Its product, based on a silyl acrylate Self-Polishing Copolymer, had not prevented a significant level of shell fouling and a dramatic increase, therefore, in hull roughness.
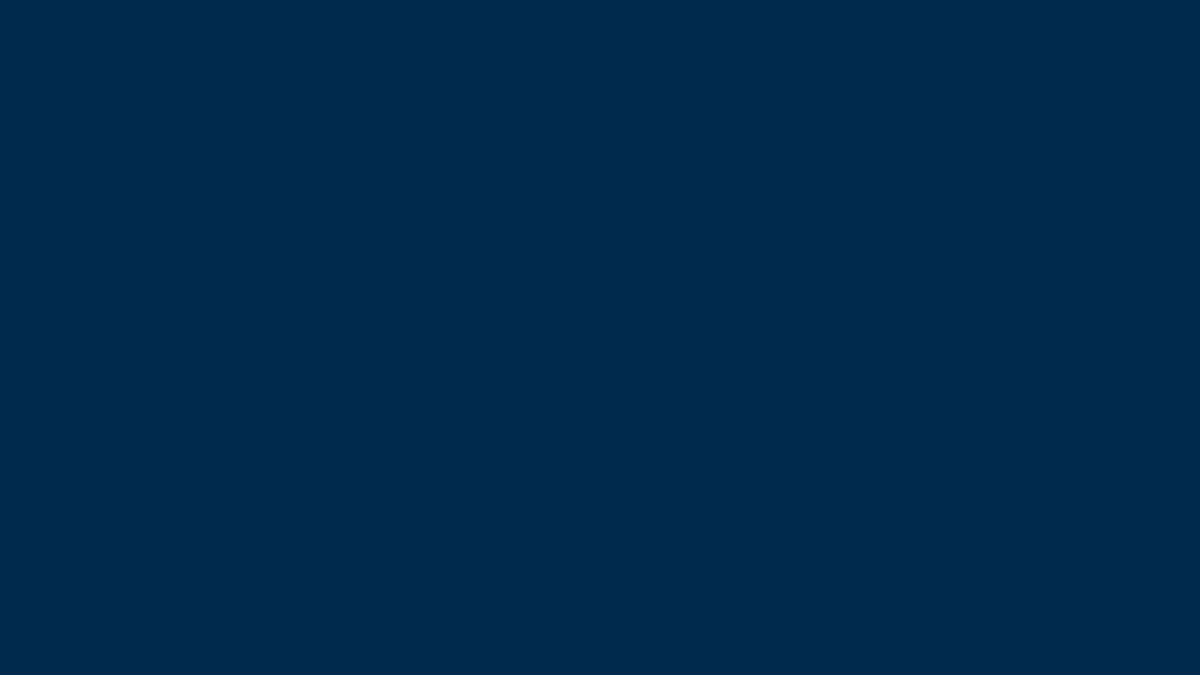
Impact of hull roughness can’t be underestimated. As a rule of thumb, every additional 25 microns of hull roughness adds 1% to hull resistance through the water. That’s why fuel consumption increases steadily between drydockings.
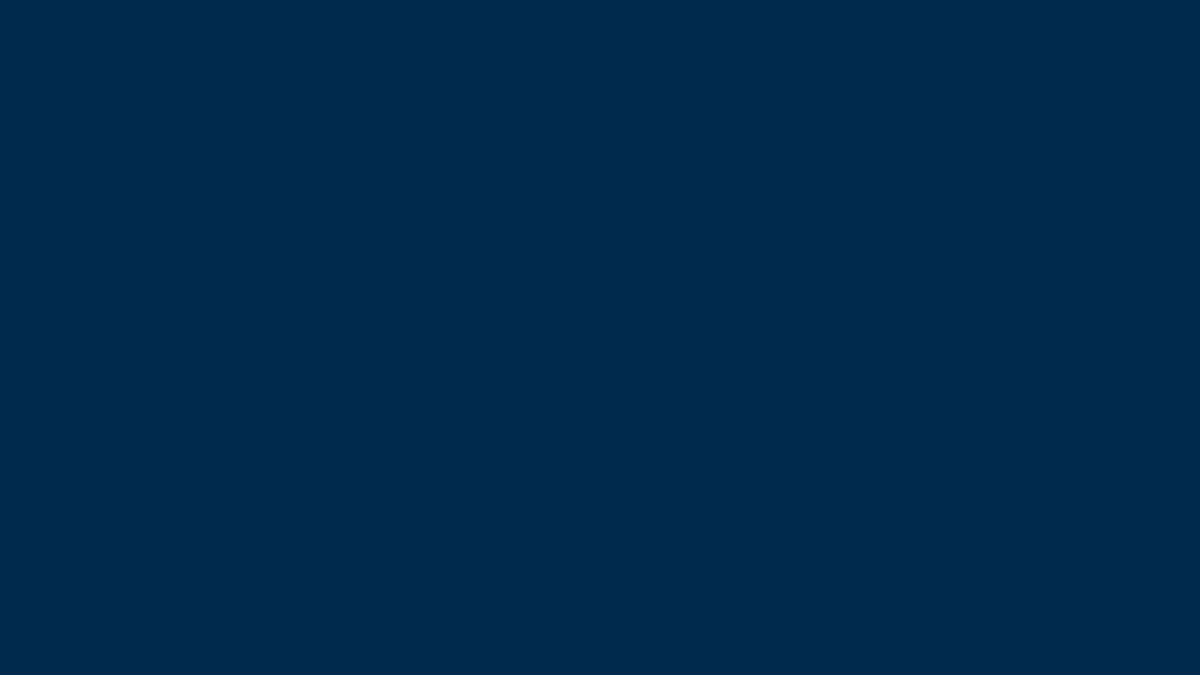
However, after a full hull blast and application of Intercept 8500 LPP in drydock, we have found very smooth hulls, much smoother, in fact, than the typical 90-100 microns that is expected to be achieved by a biocidal antifouling after a full hull blast. In some of the first applications, we recorded hull roughness levels of 46 microns, 67 microns and 89 microns. This is exceptional!
Another example of exceptional performance of Intercept 8500 LPP has been seen when applied to the hulls of offshore supply vessels working in the high fouling risk waters of the Arabian Gulf and with relatively low activity.
One owner who had a test patch on his OSV in the Gulf says its performance was excellent despite the extreme fouling challenge encountered in the Gulf and the low activity of this vessel.
He has gone on record as saying that for future dockings of vessels with similar trading profiles, his preference would be to use Intercept 8500 LPP. He is just one of a number of satisfied customers. And that is great news for us!
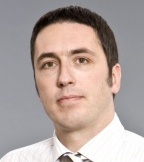
@Carl Barnes
Segment Manager - Antifouling
Contact us
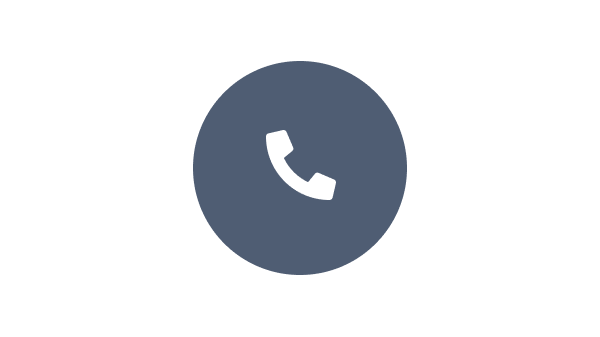
We are here to help
Speak with one of our experts to discuss how we can get the best results for your area of application.
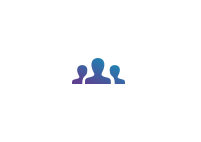
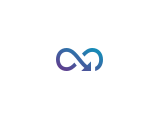
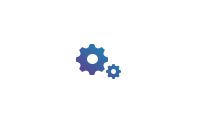