Ship operators always face a range of difficult decisions as ships head for routine dockings. Whether to spot-blast and repair existing hull coatings or pay more for a full blast and re-application of a full hull coating scheme is one of them. Smooth hulls create less frictional resistance and save fuel but comparing the relative benefits of spending more money on a full blast that will create a smooth hull compared with repairing existing coatings has been virtually impossible to estimate. Until now!
Intertrac Vision is a predictive tool, scientifically formulated and developed over four years by the Marine Coatings business of AkzoNobel, and with assistance and support from University College London, the University of Newcastle and MARIN, the ship model test basin in the Netherlands.
Using 3.5 billion datasets and 2.5 terabytes of historical coatings performance, environmental and oceanographic data gathered over more than four decades, Intertrac Vision accurately predicts “what-if’” scenarios in coating performance options over the next five-year docking cycle.
Now, for the first time, it is possible to compare the relative merits of spot-blasting versus and coating repair versus a full hull blast and a completely new hull coating scheme.
Carl Barnes, Antifouling Segment Manager at AkzoNobel explains. “Dr. Robert Townsin’s work on average hull roughness completed years ago demonstrated the importance of a smooth hull. That was the basis for our Hull Roughness Penalty Calculator which we introduced in 2003.”
“However, although we knew that a smooth hull creates less resistance and ultimately saves fuel, there was no scientific way to calculate the net present value of fuel savings over a five-year period, and therefore the payback period of spending more money up-front.”
“We would always recommend a full blast,” Barnes continues, “because you get a smoother hull and better fuel consumption. We know this works in practice too because one leading container line invariably demands a full blast on the hulls of its ships once every five years.”
To prove the point, Barnes demonstrates how Intertrac Vision can be used in a real-life example on a 13,000 TEU containership operating in the Atlantic Basin. All of the necessary variables are entered into the Intertrac Vision software, including ship dimensions, speed, utilization, fouling challenge, fuel cost and blasting and coating cost.
It is estimated that more than 60% of dockings now take place in China where blasting costs $5.5/m2, compared with $24/m2 in Singapore. Based on Chinese costs and assuming spot repairs covering 20% of the hull area, it would cost about $340,000 to spot-blast and repair hull coatings using the company’s Intertuf and Intergard anti-corrosive, tie coat and Intersmooth 7460HS SPC self-polishing copolymer antifouling.
Using the same products, a full blast would cost about $550,000. However, over a five-year docking cycle, the smoother hull would consistently require at least 3% less power for the same speed.
At an assumed bunker price of $350 per tonne, Intertrac Vision reveals a payback period of about six months, total accumulated cost savings of $2.3m and emissions savings of more than 22m tonnes of carbon dioxide over the five-year period.
Contact us
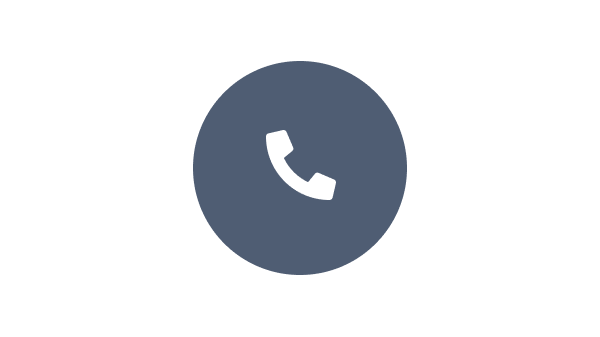
We are here to help
Speak with one of our experts to discuss how we can get the best results for your area of application.
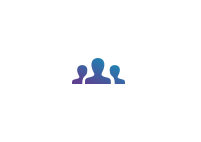
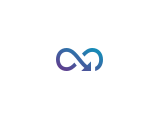
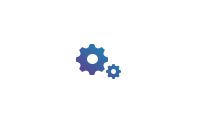