Intersmooth 7460HS SPC and Intersmooth 7465HS SPC can mean fewer coats and reduced dry dock time.
Intersmooth 7460HS SPC is designed for maintenance and repair along with Intersmooth 7465HS SPC designed for newbuilding situations. Launched in 2008 they are based on a copper acrylate Self Polishing Copolymer (SPC) technology. They are higher volume solids versions of the original Intersmooth 460 SPC and Intersmooth 465 SPC which boast a successful combined track record of over 6,500 applications to 300m DWT.
The increase in volume solids from 40% to the current 54% means less volatile organic compound (VOC) emissions which is far more attractive to shipyards seeking to meet tougher VOC emission regulations. The higher volume solids, depending on scheme life and vessel activity, can also mean fewer coats of antifouling need to be applied which can reduce time in dry dock which is critical in today’s difficult market conditions.
The current versions Intersmooth 7460HS SPC and Intersmooth 7465HS SPC now have their own impressive track record of over 4,700 applications to 208m DWT, combined with over 1,000 in service and dry dock inspections and now many of these inspections are after five years in service showing excellent performance.
Intersmooth 7460HS SPC and Intersmooth 7465HS SPC are based on copper acrylate SPC technology. This technology works by a chemical reaction with the seawater, resulting in a predictable and consistent polishing rate. This allows the products to deliver high performance, self-polishing, smoother surface, and efficient biocide delivery with a limited leach layer build-up. This predictable polishing allows for schemes up to 90 months meaning the product is particularly suitable for vessels such as containers, PPC, and PTCC vessels that are not part of the International Association of Classification Societies (IACS) enhanced survey programme which allows for 7.5 year dockings.
This long term consistent performance is in contrast to products that are based on rosin technology (Controlled Depletion Polymer, CDP), which will deliver a good cost-effective level of performance over a 3 year dry dock cycle. However, the build-up of thicker leach layers with these systems will mean fouling control is not at the same high level as SPC technology.
To prove the point, AkzoNobel’s hull performance predictive tool, Intertrac Vision can be used in a real-life example on a Capesize bulker vessel operating from China to Australia. All of the necessary variables are entered into the Intertrac Vision software, including ship dimensions, speed, utilization, fouling challenge, fuel cost, blasting and coating costs.
Based on blasting costs in China and assuming a full hull blast, it would cost about $294,000 to blast and recoat the hull using a rosin based CDP antifouling system and about $363,000 using the coper acrylate SPC Intersmooth 7460HS SPC system. However, over a three-year docking cycle, the hull coated with Intersmooth 7460HS SPC would require on average 3% less power than for a CDP coated hull.
At an assumed bunker price of $350 per tonne, Intertrac Vision reveals a payback period of about 13 months, total accumulated cost savings of $190,000 and emissions savings of more than 2,300 tonnes of carbon dioxide over the 3-year period.
Contact us
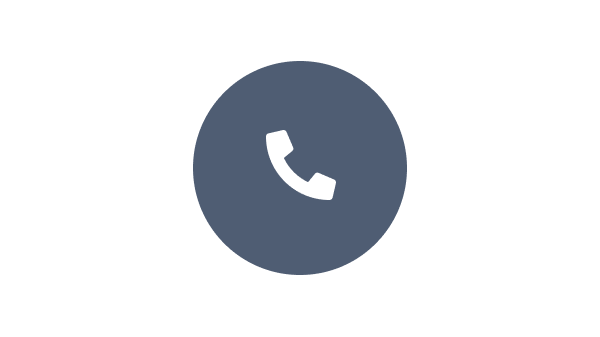
We are here to help
Speak with one of our experts to discuss how we can get the best results for your area of application.
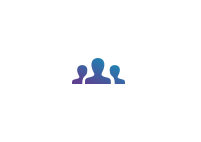
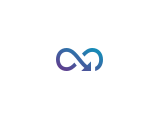
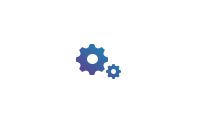