Maximising revenue streams in the complex operation of sophisticated chemical carriers is a constant challenge. The right choice of tank coating, particularly for ships engaged in the carriage of aggressive chemicals, is essential, as many operators know to their cost.
The wrong tank coating can lead to coating repair or replacement bills and off-hire running into millions of dollars. For some, the whole experience has become a nightmare – from curing and adhesion problems to cracking and cargo contamination. And in some instances, coatings company guarantees have not been honoured, resulting in costly legal disputes.
Most chemical tank coatings are based on epoxy phenolic technology and newbuilding specs have traditionally named such coatings as standard. However, this technology has certain limitations and, as a result, can restrict a ship’s earnings by cutting days on hire by several weeks each year.
Routine cleaning operations between cargoes are a constant challenge. And many existing coatings are prone to absorption and require a “recovery” period of up to two weeks between aggressive cargoes. Many such coatings are simply unsuitable for the carriage of tough chemicals and cargo owners insist on ships with stainless steel tanks.
This may not be necessary. International’s Interline® 9001 has ushered in a new era in chemical tank coating technology and is now becoming the product of choice for many operators. Some are choosing it from new; others are replacing non-performing coatings during maintenance and repair dockings.
Andrew Hopkinson is Business Development Manager at International Paint and was instrumental in the launch of Interline®9001 in 2011. Since then, he has observed the product’s steady progress as its benefits have become better known in this specialised shipping sector.
Interline®9001, he explains, has been formulated specifically to tackle the usual hassles associated with tank coating conditioning, operation and management. From the initial post-application curing process to cleaning and, crucially, cargo flexibility, Interline®9001 is streets ahead of other products.
A key issue in the tank coating sector, Hopkinson maintains, has been a lack of transparency. Coating manufacturers have exaggerated product performance and, in practice, a range of problems have been encountered. These have frequently led to costly downtime and even, in some cases, to the repeated re-coating of tanks in which coatings have failed again.
Complete transparency must provide appropriate reassurance for customers that coatings do what they say on the tin, he insists, and International’s global technical support network exists to provide after-sales service should it be necessary. Unlike any other marine coatings manufacturer, International’s support network is truly global, with more than 800 technical service representatives in most of the world’s key ports, Hopkinson points out.
Designed specifically by International chemists for use in chemical tanks where sometimes different aggressive cargoes are shipped one after the other, Interline®9001 compares well with traditional epoxy phenolics. It is suitable not only for all of the cargoes which can be carried in tanks coated with such products, but also for a range of other even more aggressive cargoes traditionally reserved for shipment in stainless steel tanks.
Interline®9001 has a range of advantages as compared with many other coatings supposedly designed to protect chemical cargoes, specifically scoring top marks for chemical resistance and cycling flexibility.
Immediately after application, for example, the curing process is simpler and saves time and money. Critical for the formulation of a tight and dense structural network, the curing procedure ensures that the coating is almost impermeable and therefore there is significantly reduced risk of cargo contamination in the future.
Interline®9001 cures between 60°C and 80°C and, for vessels capable of generating and circulating hot water, the coating can be cured between a drydocking and the first load port. This can save up to a week of additional time in dock as well as enhancing a vessel’s earning potential.
In operation, Interline® has been specially formulated for easy cleaning between cargoes, a key requirement for charterers who now have more sophisticated analytical equipment and procedures to check on the risk of cargo contamination.
The specification of cargoes themselves is getting tighter – former so-called “easy cargoes” are now classed as “high spec”, Hopkinson explains. And if there is any sign of contamination – however limited –ship operators often face considerable claims from cargo owners.
The situation is made worse because tank cleaning options are increasingly restricted on board ship. Tank washing using methanol has now been banned on health and safety grounds, and some existing and permeable coatings must be washed repeatedly to ensure that the next cargo does not become contaminated.
But Interline®9001’s composition with its tight structural network and smooth, near impermeable surface means it is easy to clean, cutting cleaning times by up to 70% compared with conventional epoxy phenolic coatings. For Hopkinson, this is a key point because, he says, cleaning tanks between cargoes is one of the main factors limiting revenue generation. Extra bunkers required for hot water on board to clean tanks could cost up to $100,000 each time, without accounting for labour costs or cleaning materials, he says. Interline®9001 saves time and fuel, raising revenue generating potential.
It is no surprise, therefore, that a growing number of chemical carrier operators are lining up to discover more about the benefits of Interline®9001. Many are considering the replacement and upgrade of existing coatings; and many more are planning to request Interline®9001 on board newbuildings.
If you are interested to hear more, please call or email Andrew Hopkinson
Telephone number: +44(191) 402 2662
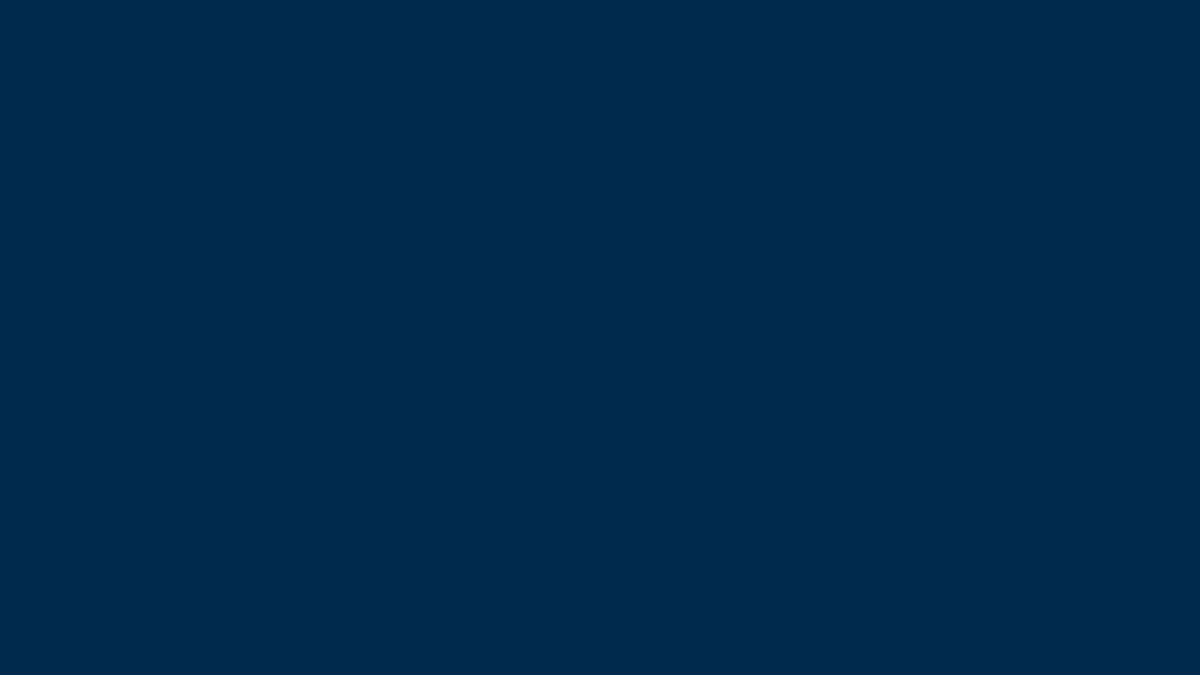
Contact us
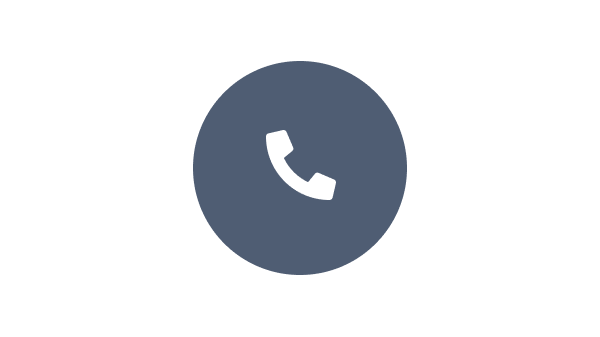
We are here to help
Speak with one of our experts to discuss how we can get the best results for your area of application.
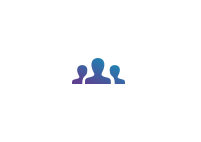
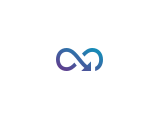
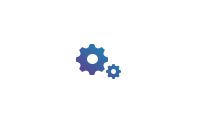